Fort Meade, MD --
During the Soviet Union’s blockade of West Berlin from June 24, 1948 to May 11, 1949, the newly created U.S. Air Force, not even a year old, executed its first major air mobility mission.
U.S. transport planes, along with Royal Air Force and British civil transport aircraft, delivered nearly 2.4 million tons of foodstuffs, coal and supplies to the beleaguered citizens of free Berlin.
But the small cargo capacity of the aircraft required around the clock flight for a solid year, nearly 300,000 in total, to keep the West Berliners alive.
While the blockade was broken and the mission declared a resounding success, the Berlin Airlift highlighted the need for the development new of heavy-lift aircraft with greater capacity and range that would allow for the U.S. military to quickly respond to a hot zone with an abundance of materiel, troops or humanitarian aid.
Replacements for the WWII-era C-47, C-46 and C-54, like the jet-powered C-141 Starlifter, fit the bill for a time, but the Vietnam War once again sent the Air Force on a search for an even longer range and larger capacity airframe.
It would take years of engine and airframe design, development and testing, accompanied by budgeting, contracting and procurement, to develop the “Global Reach” made possible by the Lockheed C-5A Galaxy, but it paid big dividends.
During the Desert Shield portion of the Gulf War beginning Aug. 7, 1990, Military Airlift Command, predecessor of today’s Air Mobility Command, used a few dozen C-5 and C-141B aircraft to move the 1st Tactical Wing and the 2,300 troops and supplies of the 82nd Airborne’s “Ready Brigade” into position to defend Saudi Arabia from Iraqi attack just 18 hours after the president’s go order.
Within days, 265 C-141B Starlifters and 85 C-5 Galaxies began landing at Dhahran Air Base, Saudi Arabia every seven minutes. The Desert Shield lift exceeded the tonnage of the 11-month Berlin Airlift of 1948-49 in just 22 days. By October 1990, 220,000 troops and their equipment, weapons, building material, tanks and vehicles were in the area of operations; the greatest and swiftest military buildup in the Air Force’s 70-year history.
Advancements in engine technology and aircraft design may lead to new heavy lift capabilities to further increase the range, delivery speed and capacity of the Air Force’s Global Reach.
But what if, in the next 70 years, the dependency on airborne “Global Reach” could be eased by a new priority: “Global Already There”?
Currently, before material assets can be delivered to the field and benefit the operational needs of commanders, those assets must be designed, tested and procured by the Air Force, then built, delivered, tested operationally and deployed – a process that can be both lengthy and expensive.
In this “classic” design and delivery paradigm, the Air Force is a “customer” with a need for an asset, be it a part or an entire aircraft, to address a current or projected operational scenario.
From that need, researchers postulate and evaluate different methods to go about achieving mission success, termed “operations analysis,” and then compile the capability requirements for a new system that will meet the customer’s needs.
Those system requirements are then handed off to designers and engineers who develop prototypes which are tested and evaluated by the customer. If the customer accepts the design, there is still the time and expense of budgeting, awarding contracts, building, operationally testing and deploying the asset.
By the end of this process, years or decades may have passed, operational scenarios may have changed and budgets may have been reduced, realigned or eliminated completely.
The Air Force has worked diligently to streamline and accelerate the design, development and procurement process, but the “classic” paradigm’s multiple steps, involving multiple players both inside and outside the Air Force, is inherently limited in its efficiency.
Researchers at the Air Force Research Laboratory (AFRL) at Wright Patterson Air Force Base in Dayton, Ohio are pursuing a new paradigm, called “effectiveness based design,” that would greatly reduce asset design and development costs, and give Airmen in the field the ability to produce assets which address the immediate operational needs of a constantly fluid battlefield environment.
The new paradigm would create a relatively seamless flow from operational need, to systems design, to onsite production of an asset or part via a marriage of big data, computer-aided design (CAD) and three-dimensional (3-D) printing.
“What we’re doing is we’re linking the operational analysis assessment and the computational design phase of a new asset, be it a weapons system or a new vehicle, some small scale UAV, maybe even a large-scale manned asset, with the phase of acquiring that asset.” said Ed Alyanak, an engineer with the Aerospace Systems Directorate at AFRL.
Traditional manufacturing is a subtractive process, beginning with cutting a lump of material to create a needed part. Three dimensional printing, one type of a larger set of techniques labeled additive manufacturing, extrudes or prints a base material in layers, directed by a CAD file, to create a 3-D solid.
Three-dimensional printers at AFRL can extrude multiple materials simultaneously to create a single form with functionality integrated into the asset.
One asset recently produced is a morphing wing with movable control surfaces incorporated into the unit as a whole, instead of being a collection of separately manufactured and installed components.
Greg Reich, a research team lead in the Aerospace Systems Directorate, said the morphing wing has electrical conductivity capabilities and eventually will include integrated sensors.
“Rather than having electronics added, either as wires or wire bundles, after the model’s been made, you print them directly into the model,” Reich said. “Our 3-D printers are not just printing one material, they’re actually (printing) multiple materials, and so you have the capability of creating very complex structures, not just geometries. Now very complex systems with different materials and different functionality can be built into those models.”
The ability to print an entire structure like the morphing wing, with necessary electronics and sensors embedded, reduces cost and is time efficient.
Instead of inspecting and maintaining wear points, such as joints, hinges and mechanical actuators composed of separate parts contracted to a supplier, manufactured and then shipped, a damaged or worn wing can simply be reprinted in a matter of hours, on site.
It is a concept already proven during day-to-day aerodynamic testing at the AFRL.
“One thing that we’re working on is using 3-D printing for doing aero-elastic models,” said Reich. “They are scale models of real airplanes that retain the physical characteristics of the full-scale aircraft.”
“Traditionally, these models are very expensive, they’ll cost hundreds of thousands of dollars to make and require six months or even a year to fabricate,” Reich added. “We’ve been able to show that you can fabricate them entirely out of 3-D printed parts, no fasteners, in a very inexpensive and a very fast method. “Each of our models cost $2,000 and take about a day to reprint. We recently tested 5 models to failure in a one-week testing period. Five of our traditional models would have cost millions of dollars and could never be constructed in such a short period of time.”
According to Reich, the promise of 3-D printing technology, coupled with Alyanak’s blend of operational analysis and design phases, may lead to a radical change in the way the U.S. Air Force supports its mission in the next 70 years.
“Currently, a lot of the stuff we’re doing is small scale UAVs or wind tunnel test model assets, but there have been universities that have 3-D printed complete aircraft and flown them successfully,” said Alyanak. “We’re just bringing this technology forward on steroids. Right now we are talking about smaller-scale or medium-scale assets, but there’s no reason that in 70 years, this technology couldn’t build assets on the scale of 50,000 pounds, where you’re in a manned-fighter class capability. That is the vision for these technologies and how they work together.”
Reich envisions a time when the physical 3-D process will be a self-contained system with a collection of stock materials that could fit in the back of a van, semi-truck or shipping container.
“You would have the ability to create systems in the field,” said Reich. “If you can computationally define what they are, and you have the ability to fabricate them, now you can create an entire system, an entire weapon’s system, from the ground up, in the field, complete with all the functionality – electrical, structural, sensor, communications, directly built in, in one shot That’s a huge advance.”
Some even envision a time when algorithms – bolstered by advances in machine learning where computers learn from their successes and mistakes to constantly build capability – allow an Airman to simply enter mission requirements into the system and the computer would produce a CAD file of a suggested asset which the Airman could reject, augment or print.
However, Alyanak maintains that within the next 70 years Airmen and engineers will still be integral to the process.
“A lot of the mathematics and engineering is going to be done behind the scenes; stress analysis, loads analysis … and put in some type of structural analysis software,” said Alyanak. “The Airman is going to define the mission requirements with the help of the computers doing the operational assessment … I think once the technology is fielded, obviously there’s going to be a learning curve, but Airmen are already involved in operational analysis and that’s not going to change. Computers aren’t going to spit out, ‘Hey, this is what you need to do your job.’”
“We have lots of computational design power; enormous computers all working on these problems, but they can’t solve the problem,” Alyanak said. “They combine a lot of information and they condense it down to a smaller amount of information that a human can understand and make decisions on. I don’t ever see Terminator-type scenarios where computers can go and execute everything and humans won’t be in the loop.”
In addition to fabricating completely new assets, 3-D printing in the area of operations could lead to a reduction in, or even elimination of, the cost of asset downtime, procurement and contracting, logistics, processing, delivery and manning associated with the traditional manufacture of replacement parts, or the need to strip parts from decommissioned assets in a “boneyard.” According to Alyanak it is process that has already being implemented.
“A lot of that can be done with a 3-D printing technology on a small component level now,” said Alyanak. “It’s being used to refurbish parts and build parts for the A-10 right now, to keep that aircraft fielded. It’s not a stretch to think that you can grow a whole airframe. “
Further reduced would be the operational risk to Airmen and aircraft, time, cost and manning needed to schedule, load, fly and refuel aircraft as well as offload assets or parts at forward bases.
Even the need to contract with the locals in an area of operation for things like trucks, trailers, tables and chairs could be eliminated.
In 70 years, an explosive ordnance disposal technician, or other battlefield Airman, could simply print a replacement piece of a kit from a computer database. An aircraft maintainer could print needed parts right on the flightline or in a backshop with no inventory worries or procurement delays. This creates a solution in a matter of hours, or even minutes, satisfying an operational need, or returns an existing piece of equipment to operational status.
For now, until someone figures out how to 3-D print pizzas, antibiotics or Airmen, there will always be a need for the Global Reach supplied by military transport, but the advent of “Global Already There” will surely ease that load.
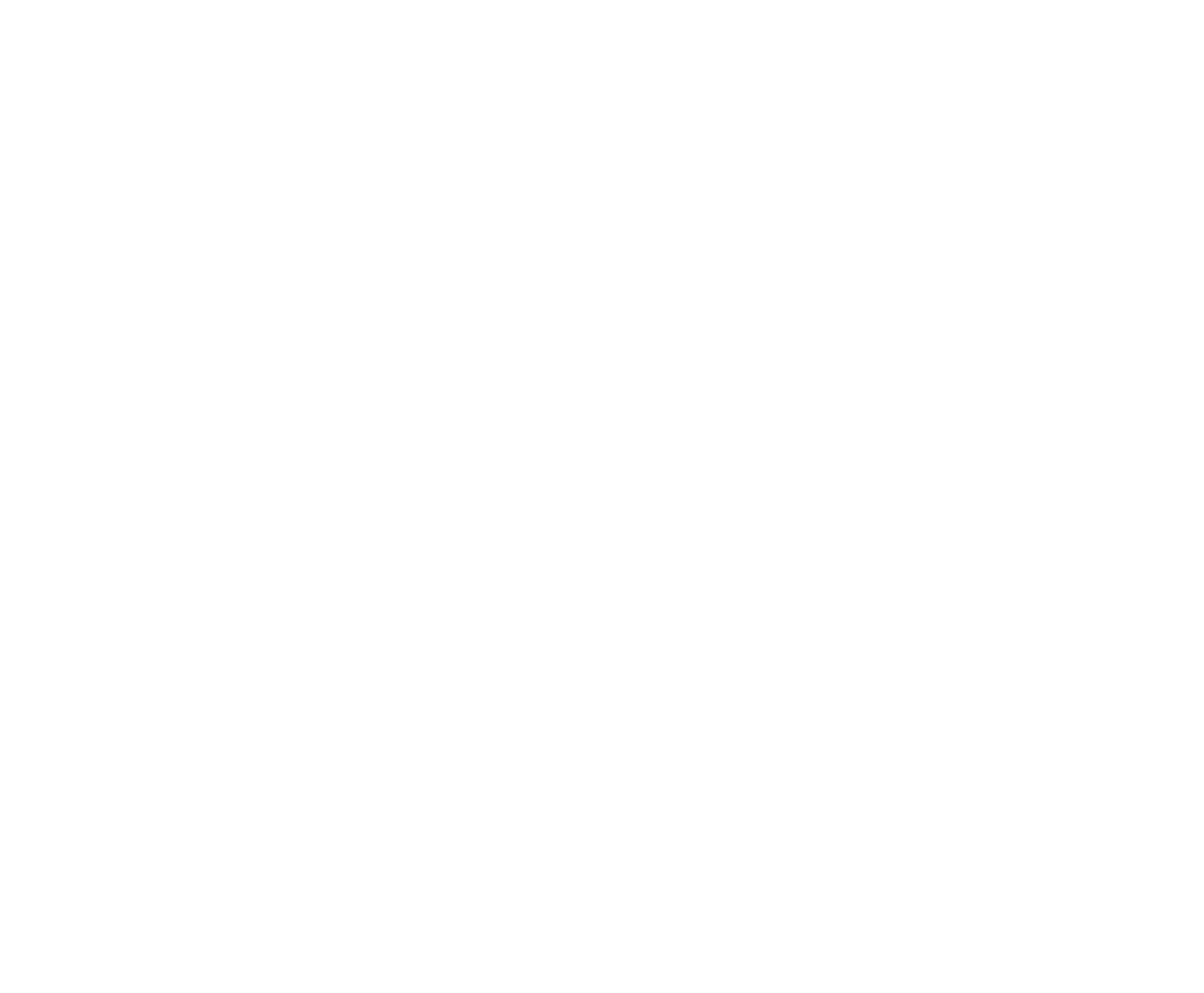